Removing
- Reduce the pressure in the fuel system.
Warning. Before disconnecting the fuel lines, reduce the pressure in the fuel system, otherwise pressurized fuel will flow rapidly from the fuel system.
- Turn out bolts and remove an engine cover.
- Remove the air filter.
- Removing the fuel pressure regulator.
- Disconnect the wiring harness connector from the fuel pressure sensor and remove the wiring harness clamp bolt (pic. 6.33).
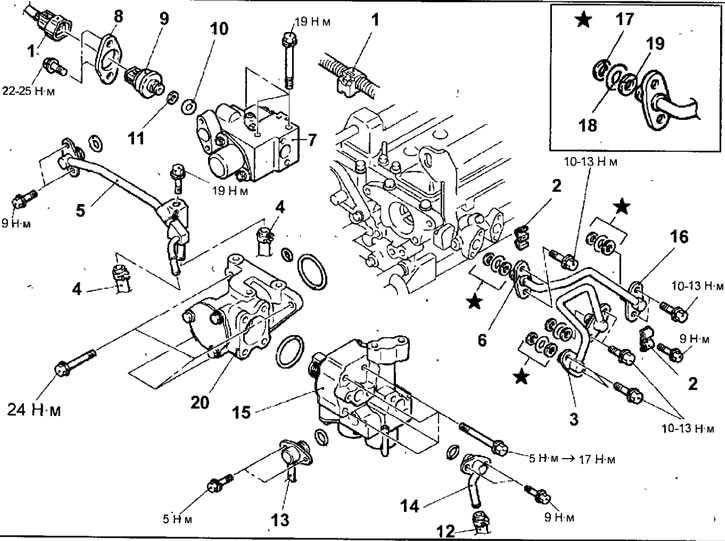
Pic. 6.33. High pressure fuel pump engine from 1999 release: 1 - wiring harness connector; 2 - clamp (fuel line fasteners); 3 - fuel supply pipe; 4 - fuel return hose; 5 - low pressure fuel pipe; 6 - fuel return pipe; 7 - fuel pressure regulator (high pressure side); 8 - flange; 9 - pressure / fuel sensor; 10 - sealing ring; 11 - Support ring; 12 - fuel return hose; 13 - fuel hose; 14 - fuel pipe; 15 - high pressure fuel pump; 16 - fuel return pipe; 17 - support ring A; 18 - sealing ring; 19 - support ring B; 20 - high pressure fuel pump crankcase
- Loosen the clamps and disconnect the fuel return hoses.
- Loosen the bolts and remove the low pressure fuel pipe
- Turn out bolts and remove a tube of return of fuel.
- Turn out bolts and remove a regulator of pressure of fuel (high pressure side).
- If the fuel pressure sensor will be re-installed, mark and mark the relative position of the flange and the sensor before removing the flange (pic. 6.34). Turn out bolts and remove a flange of fastening of the gauge of pressure of fuel.
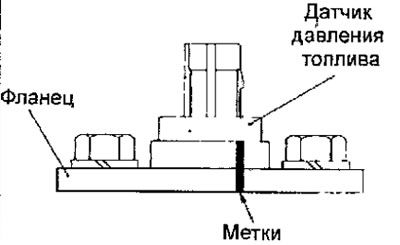
Pic. 6.34. The location of the marks that determine the relative position of the flange and the fuel pressure sensor
Note. When tightening the mounting bolts, the flange is deformed, as a result of which the sealing condition and the installation position of the sensor will be maintained in good condition. Therefore, it is necessary to apply alignment marks in order to install the flange and the sensor in the original position. When replacing the fuel pressure sensor, the flange must also be replaced.
- Remove the fuel pressure sensor.
- Loosen the clamps and disconnect the fuel return hoses.
- Loosen the bolts and remove the low pressure fuel pipe
- Turn out bolts and remove a tube of return of fuel.
- Turn out bolts and remove a regulator of pressure of fuel (high pressure side).
- Turn out bolts and remove a flange of fastening of the gauge of pressure of fuel.
- Remove the fuel pressure sensor.
- Removing the high pressure fuel pump
- Remove the throttle body.
- Turn out bolts and remove clips of fastening of fuel lines.
- Turn out bolts and remove a tube of giving of fuel.
- Loosen the clamp and disconnect the fuel return hose from the nozzle.
- Turn out bolts and disconnect a fuel hose from the fuel pump of a high pressure.
- Turn out bolts and disconnect a fuel branch pipe from the fuel pump of a high pressure.
- Turn out bolts and remove the fuel pump of a high pressure.
- Removing the high pressure fuel pump housing.
- Turn out bolts and remove a regulator of pressure of fuel (high pressure side).
- Turn out bolts and remove the fuel pump of a high pressure.
- Turn out bolts and disconnect a tube of return of fuel.
- Turn out bolts and remove a case of the fuel pump of a high pressure.
Installation
- Installation is carried out in the reverse order of removal, taking into account the following.
- Installing the crankcase of the high pressure fuel pump
- Set the piston of the 1st cylinder to TDC on the compression stroke.
- Align the match marks on the injection pump housing and coupling, then install the injection pump housing on the engine (pic. 6.35).
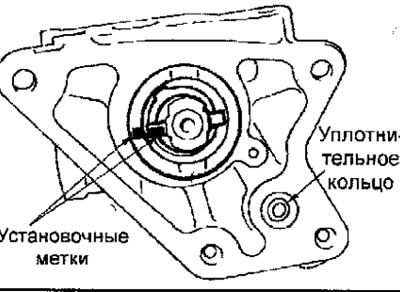
Pic. 6.35. Combination of installation (1 marks on the crankcase of the fuel pump) high pressure and coupling
Warning. Before installation, be sure to check the presence of the O-ring in the high pressure fuel pump crankcase and do not drop the ring when installing the crankcase.
Installation of support rings (A and B) sealing ring
- Establish basic rings and a sealing ring as it is shown in drawing 6.36.
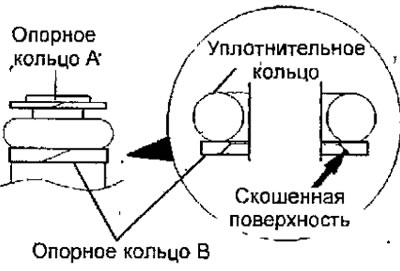
Pic. 6.36. Mounting position of support rings and sealing ring
Warnings
- 1. Install support ring B so that the beveled surface of the ring is on the side opposite the O-ring.
- 2. Make sure that the support ring A is installed correctly (the outer diameter of the support ring A is 14.8 mm). Do not confuse it with the pressure sensor support ring.
Installing fuel supply and return pipes and low fuel pressure pipes
- When installing the fuel pipes, lubricate the O-ring with a small amount of clean engine oil (pic. 6.37).
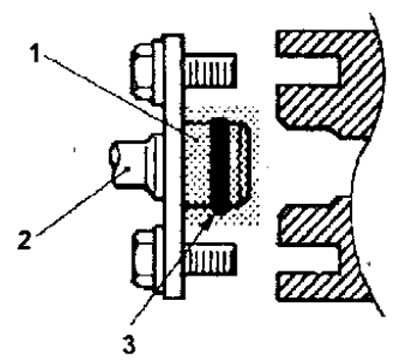
Pic. 6.37. High pressure fuel hose installation: 1 - place of lubrication with engine oil; 2 - fuel pipe; 3 - ring gasket
Warning. Do not allow oil to enter the fuel pump, fuel pressure regulator and fuel line.
High pressure fuel pump installation
To tighten the fuel pump mounting bolts, use a torque wrench that tightens to an accuracy of 0.5 Nm. Tighten the fuel pump mounting bolts in the sequence shown in Figure 6.38 as follows.
- 1. Tighten the bolts to 5 Nm.
- 2. Tighten the bolts to 17 Nm. The torque difference between the four bolts must not exceed 2 Nm.
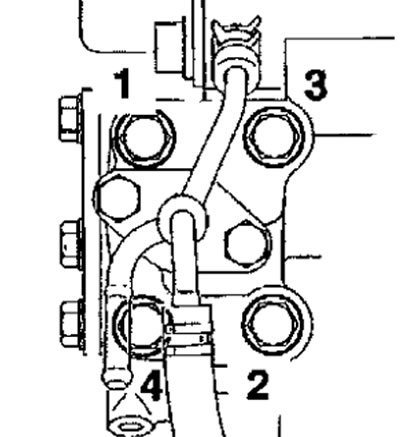
Pic. 6.38. Fuel pump tightening sequence
Fuel hose installation
- When installing the fuel hose, lubricate the O-ring with a small amount of clean engine oil. Do not allow oil to enter the fuel pump.
- Slightly turning the fuel hose flange to the right or left, carefully insert it into the fuel pump so as not to damage the O-ring. After installation, check that the hose turns smoothly in the fuel pump.
- If the hose flange sticks when turning, the cause may be a damaged O-ring. Detach the flange (complete with hose) from the fuel pump and check the gasket for damage, then put it back in and check for smooth turning.
Installing the Fuel Pressure Sensor Support Ring
- Install the support and sealing rings on the fuel pressure sensor as shown in Figure 6.39.
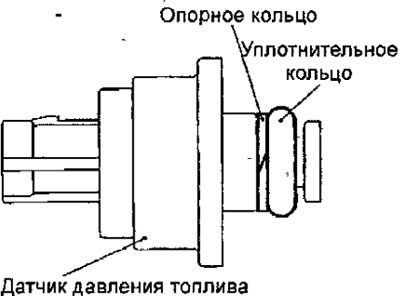
Pic. 6.39. Mounting position of support and sealing rings
Warning. Make sure the support ring is installed correctly (the outer diameter of the support ring A is 15.1 mm). Do not confuse it with the support ring of the injector, fuel supply pipe and fuel return pipe.
Installing the Fuel Pressure Sensor and Flange
- Lubricate the O-ring of the fuel pressure sensor with engine oil. Do not allow oil to enter the fuel pressure regulator.
- Align the marks made before removing the sensor, and install the fuel pressure sensor and flange on the fuel pressure regulator.
Warning. When replacing the fuel pressure sensor, also replace the flange.
- Bleeding air from the high pressure fuel pump
- Start the engine and let it run for two minutes at a crankshaft speed of 2000 min-1, This will bleed air from the fuel pump.
Note. Air can enter the fuel pump when it is removed. If air enters the pump, fault code 56 will be displayed.
- Use the MUT-II to confirm the DTC. If fault code 56 is stored in the memory of the engine control unit, erase it.