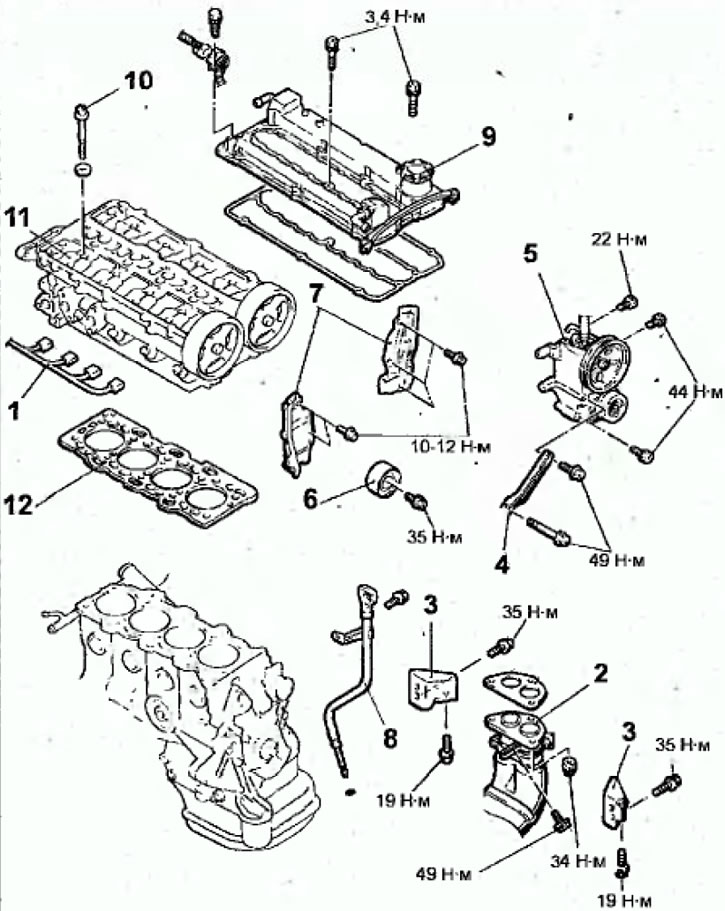
Pic. 2.35. Engine cylinder head from 1999 release: 1- electrical connectors of the injector wiring harness; 2 - intake exhaust pipe; 3 - exhaust manifold bracket; 4 - power steering pump support bracket; 5 - power steering pump and bracket; 6 - idle pulley; 7 - rear casings of the toothed belt; 8-guide tube for engine oil level indicator; 9 - cylinder head cover; 10 - cylinder head bolt, 74 Nm + loosen + 20 Nm + 90°+90°; 11 cylinder head assembly; 12 - cylinder head gasket.
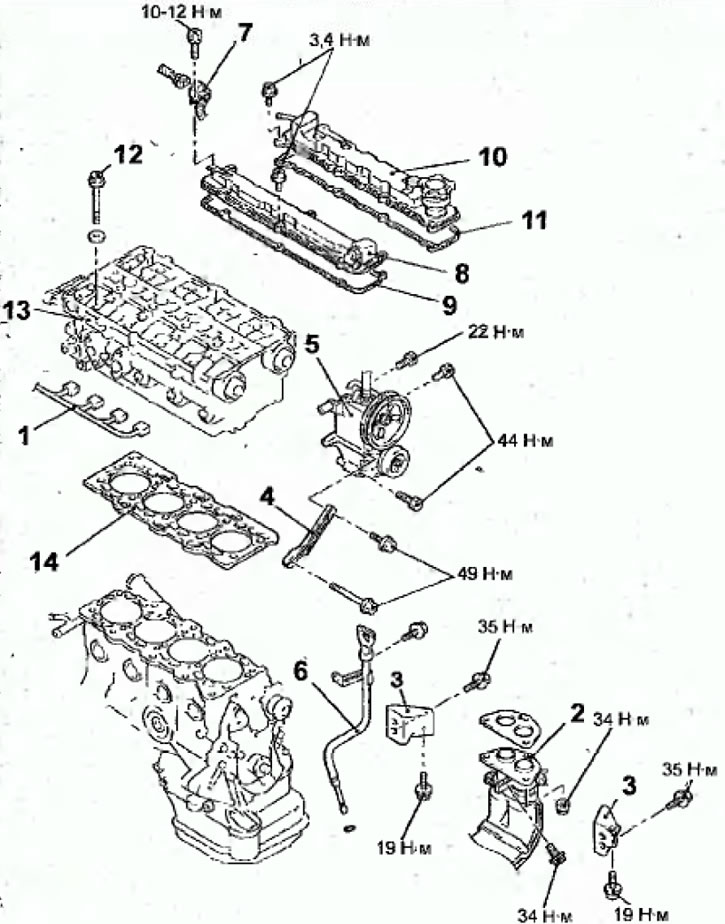
Pic. 2.37. Engine cylinder head from year 2000: 1 - injector wiring harness connector; 2 - intake exhaust pipe; 3 - exhaust manifold bracket; 4 - support bracket for the power steering pump; 5 - power steering pump and bracket; 6 - guide tube of the engine oil level indicator; 7 - injector wiring harness bracket, 8 - cylinder head cover (release side); 9 - cylinder head cover gasket; 10 - cylinder head cover (release side); 11 - cylinder head cover gasket, 12 - cylinder head bolt, 74 Nm + loosen + 20 Nm + 90°+ 90°, 13 - cylinder head assembly, 14 - cylinder head gasket
Parts of the gas distribution mechanism are installed and work in the cylinder head. To improve thermal conductivity and reduce weight, the cylinder head is made of light alloy. It is exposed to high temperatures and gas pressures and therefore has a rigid lower support surface and is intensively cooled by liquid, and the wall thickness is made as uniform as possible in order to reduce internal stresses from thermal expansion. The valve seats are pressed into the heated cylinder head and after it cools down, a stronger, more reliable connection is obtained. Each combustion chamber has threaded holes for spark plugs. The threads in the holes can be damaged if the spark plug is overtorqued or if it is screwed in and overtorqued.
The gasket between the engine block and the head is designed to keep the combustion chambers and coolant passages separated from each other, while it must not let engine oil in and must withstand high temperature and pressure fluctuations.
Removing
- Disconnect the wire from the negative battery terminal.
- Reduce the pressure in the fuel system.
- Drain the coolant from the cooling system.
- Remove the plug and drain the engine oil from the engine.
- Remove the timing belt drive timing.
- Remove the intake manifold.
- Remove the high pressure fuel pump and fuel pressure regulator, and use a towel or rag to collect the leaked fuel.
- Remove the LGR valve.
- Remove the thermostat and upper radiator hose.
- Disconnect the electrical connector from the fuel injectors.
- Loosen the nuts securing the exhaust manifold flange to the exhaust manifold.
- Turn out a bolt and disconnect a reception exhaust pipe from a final collector.
- Turn out bolts and remove an exhaust manifold bracket.
- Loosen the bolts and remove the power steering pump with attached hose and bracket.
Note. Secure the removed power steering pump to the engine compartment with a cord or soft wire so that the ohm does not interfere with the removal of the cylinder head.
- Loosen the bolt and remove the idler pulley.
- Turn out bolts and remove back casings of a gear belt.
- Turn out a bolt and remove a directing tube of the index of level of engine oil together with a sealing ring.
- Turn out bolts and remove a cover of a head of cylinders.
- Using a special tool for 2 or 3 approaches in the sequence shown in Figure 2.36, loosen and unscrew the cylinder head bolts
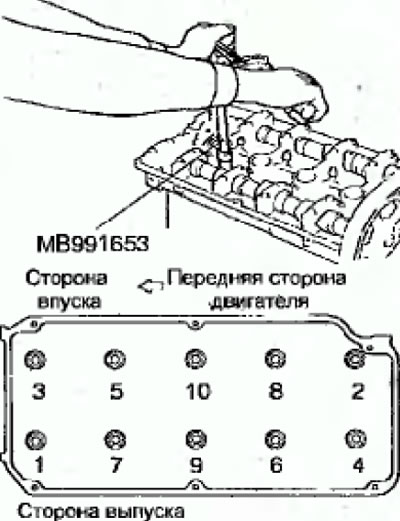
Pic. 2.36. The sequence of turning out the bolts of the cylinder head
- Carefully remove the cylinder head.
- Remove the cylinder head gasket.
- Cover the engine cylinders with a clean, lint-free cloth.
Preparing for installation
- The mating surfaces of the head and cylinder block must be perfectly clean. Use a hard plastic or wooden scraper to clean them. Be careful when cleaning as aluminum alloy is very easy to damage. Check that carbon deposits do not get into the oil and water channels. This is especially important for the lubrication system, as deposits can block the oil supply to engine components. Clean channels if necessary.
- Check the mating surfaces of the cylinder head and block for nicks, deep scratches and other damage. If the defects are small, remove them by machining. But in case of significant defects, the parts must be replaced.
- With a metal ruler and probes in six directions, check the flatness of the cylinder head. Regrind the cylinder head if necessary.
- Using a metal ruler and a feeler gauge, measure the flatness of the mating surfaces of the collectors in two directions.
- Clean the bolt holes in the cylinder block. Driving a bolt into an oil-filled hole may rupture the block due to hydraulic pressure.
Installation
Installation is carried out in the reverse order of removal, taking into account the following.
- Degrease the mating surfaces of the blocks and cylinder heads.
- When installing, check that all holes on the gasket and cylinder head match
- Install the gasket and cylinder head to the cylinder block
- Check the condition of the cylinder head bolts and especially their threads. Measure the length of each bolt (without puck) from the underside of the bolt head to the end of the bolt. If the bolt length (Ah, fig. 2.38) less than 96.4 mm, they can be reused. If any bolt is longer than specified, shade all bolts in the kit.
- Install washers on the cylinder head under the head mounting bolts, rounded side up, as shown in Figure 2.38.
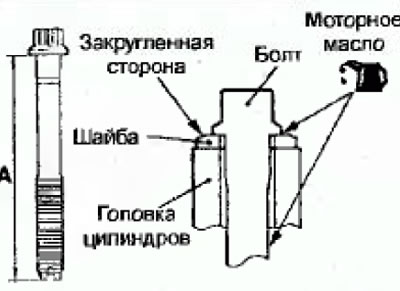
Fig. 2.38. Arrangement of a bolt and a washer of fastening of a head of cylinders: And = 96,4 mm
- Lubricate the top surface of the washer and bolt threads with engine oil before installing.
- Tighten the cylinder head bolts in several stages in the sequence shown in Figure 2.39.
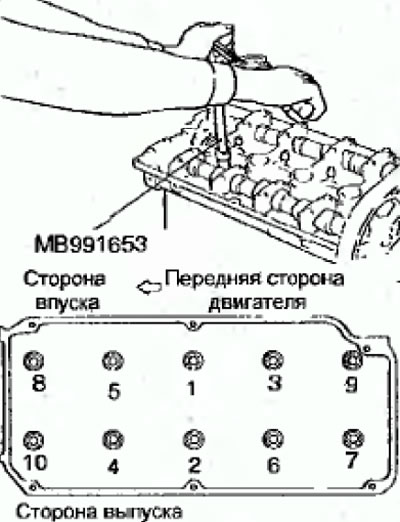
Pic. 2 39. Cylinder head bolt tightening sequence
Bolt tightening steps:
- step 1: tighten to 74 Nm
- Step 2: Completely loosen all bolts in the reverse order shown in Figure 2.39
- step 3: tighten to 20 Nm
- Step 4: Tighten the bolts by 90°. Apply paint marks on the bolt heads and cylinder head (pic. 2.40)
- Step 5: Tighten the bolts an additional 90°. The marks on the bolts and the cylinder head must be in line (pic. 2.40)
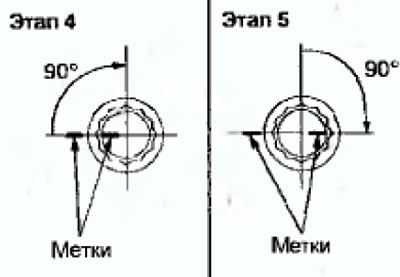
Pic. 2.40. Turning the cylinder head bolts
Warnings
(1) Always tighten the bolt at a strictly 90°angle, otherwise the cylinder head bolt may be loosened (the reliability of the gas connection will not be ensured)
(2) If the bolt is turned more than 90°, loosen it completely and repeat all bolt tightening operations
- Install the cylinder head cover and secure with bolts, tightening them to the required torque.
- Install the engine oil gauge guide tube with a new O-ring and secure with the bolt
- Install the rear toothed belt guards.
- Install the idler pulley and secure with the bolt, tightening it to the required torque.
- Install the power steering pump bracket.
- Install the exhaust manifold bracket and secure with the bolts, tightening them to the required torque.
- Install the exhaust pipe flange to the exhaust manifold and secure with nuts, tightening them to the required torque.
- Install the upper radiator hose and thermostat.
- Install the EGR valve.
- Install the fuel pressure regulator and high pressure fuel pump and secure with bolts to torque.
- Install the intake manifold.
- Install the timing belt drive of the gas distribution mechanism.
- Fill the engine with the required amount of recommended engine oil.
- Pour coolant into the cooling system
- Connect the wire to the negative battery terminal.
- Start the engine and check for leaks.