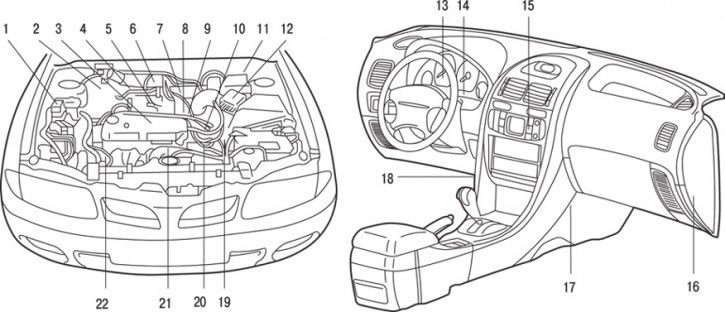
Pic. 7.1. Location of elements of the SOHC injection system: 1 - relay of the electromagnetic clutch of the air conditioner compressor; 2 - solenoid valve purge adsorber (for right hand drive vehicles); 3 - knock sensor; 4 - service connector of the fuel pump; 5 - nozzles; 6 - electromagnetic atmospheric valve (vehicles with TCL system); 7 - throttle position sensor (for vehicles with TCL system); 8 - idle speed regulator of the crankshaft of the engine (ISC servo); 9 - accelerator pedal position sensor (with sensor-switch of the fully closed position of the throttle valve) (vehicles with TCL system); 10 - ignition distributor (with ignition coil, power transistor, TDC sensor and crankshaft position sensor); 11 - solenoid valve purge adsorber (for left hand drive vehicles); 12 - air flow meter sensor (with intake manifold air temperature sensor and atmospheric sensor (barometric) pressure; 13 - vehicle speed sensor; 14 – a control lamp of malfunction of the engine; 15 - air conditioner switch; 16 - electronic engine control unit; 17 - control relay (control relay); 18 - diagnostic socket; 19 - starter interlock switch (automatic transmission selector switch); 20 - coolant temperature sensor; 21 – oxygen concentration sensor; 22 - sensor (sensor-switch) fluid pressure in the hydraulic system of the power steering
The distributed fuel injection system consists of sensors and actuators operating on commands from the engine control unit (engine-ECU). Sensors register the state of the engine and transmit information to the electronic control unit, on the basis of which the unit controls the operation of the engine. The location of the elements of the SOHC and DOHC injection system is shown in fig. 7.1 and 7.2.
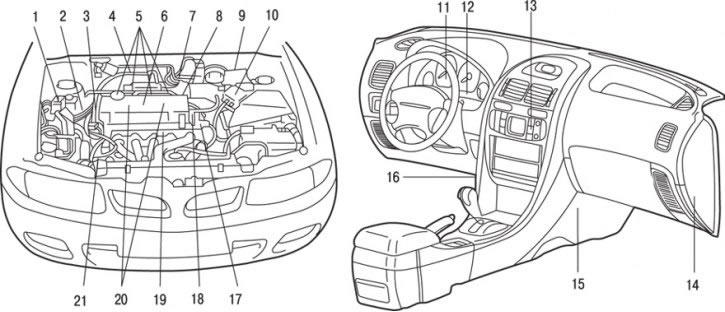
Pic. 7.2. Location of elements of the DOHC injection system: 1 - relay of the electromagnetic clutch of the air conditioner compressor; 2 - crankshaft position sensor; 3 - camshaft position sensor; 4 - service connector of the fuel pump; 5 - nozzles; 6 - knock sensor; 7 - throttle position sensor (with sensor-switch of the fully closed position of the throttle valve); 8 - idle speed regulator of the crankshaft of the engine (ISC servo); 9 - solenoid valve purge adsorber (vapor recovery system); 10 - air flow meter sensor (with intake manifold air temperature sensor and atmospheric sensor (barometric) pressure); 11 - vehicle speed sensor; 12 – a control lamp of malfunction of the engine; 13 - air conditioner switch; 14 - electronic engine control unit; 15 - control relay (control relay); 16 - diagnostic socket; 17 - coolant temperature sensor; 18 - ignition system malfunction sensor; 19 – oxygen concentration sensor; 20 - ignition coils; 21 - sensor (sensor-switch) fluid pressure in the hydraulic system of the power steering
The unit controls fuel injection, idle speed and ignition timing. In addition, the control unit has a number of diagnostic modes of operation to simplify troubleshooting.
The moment of injector opening and the duration of its open state are set in such a way that the engine receives an air-fuel mixture of optimal composition, corresponding to continuously changing engine operating conditions.
The injector is installed on the inlet pipe of each cylinder. Pressurized fuel is supplied by the fuel pump from the tank to the fuel rail. The pressure is maintained by a pressure regulator. In the fuel rail, fuel at a certain pressure is distributed to each nozzle.
Under normal conditions, fuel is injected once every two revolutions of the crankshaft for each cylinder.
The order of operation of the cylinders: 1–3–4–2. This mode is called sequential fuel injection. The electronic control unit provides an enrichment of the air-fuel mixture during engine warm-up, as well as during operation at maximum load, controlling without feedback on the composition of the mixture («open-loop»).
If the engine is warm or running in partial modes, then the control unit ensures that the stoichiometric (theoretically necessary for the complete combustion of fuel) composition of the air-fuel mixture, exercising feedback control («closed-loop») on the composition of the mixture using the signals of the oxygen concentration sensor. This ensures maximum efficiency of the three-way catalytic converter.
The electronic engine control unit maintains the optimum idle speed, depending on external conditions and engine load, by regulating the amount of air entering the engine through the bypass passage, bypassing the throttle valve. The engine control unit controls the idle speed control servo (ISC), ensuring that the set speed is maintained depending on the temperature of the coolant and the load from the air conditioner. In addition, when the air conditioner is turned on and off while the engine is idling, the idle speed control stepper motor (ISC) doses the amount of additional air in such a way as to exclude fluctuations in the speed of the crankshaft.
A power transistor connected to the primary circuit of the ignition coil closes and opens the circuit. In this way, the ignition timing is optimally controlled according to the engine's operating conditions.
The electronic engine control unit determines the optimum ignition timing depending on the engine speed, the volume flow of air entering the engine, the temperature of the coolant and atmospheric pressure.
The fuel tank is located under the floor of the rear seats to provide passive safety and increase the volume of the luggage compartment.
To prevent leakage of fuel from the tank in the event of an accident (car flip) a fuel cut-off valve is installed in the fuel vapor line.
In order to reduce weight and increase corrosion resistance, the fuel tank is made of plastic.