Removing
Before you start removing parts, do the following:
- A) Unscrew the drain plug and drain the oil from the gearbox housing.
- b) Remove the elements of the exhaust system (see chapter "Intake and exhaust systems").
- V) Remove the rear drive shafts (see section "Rear drive shafts").
- G) Remove the rear anti-roll bar (see chapter "Suspension").
Removal of parts is carried out in the order of the numbers indicated in the figure "Removing the rear gear". When removing parts, pay attention to the operation of detaching the cardan shaft.
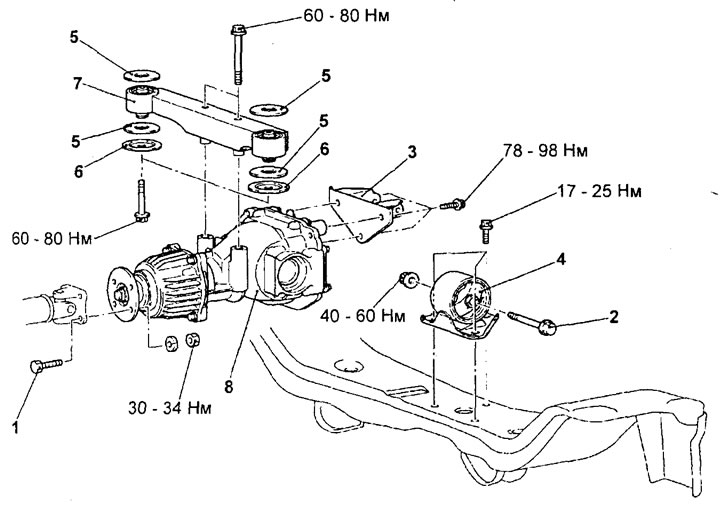
Removing the rear gear. 1 - cardan shaft mounting bolt, 2 - support mounting bolt, 3 - gearbox bracket, 4 - gearbox mounting support, 5 - washer, 6 - limiter, 7 - gearbox mounting beam, 8 - reducer assembly.
Loosen the bolts and disconnect the cardan shaft, then hang it on the wire without lowering it down.
Examination
Attach special tool (support stand) in a vise and install the gearbox assembly in the special tool.
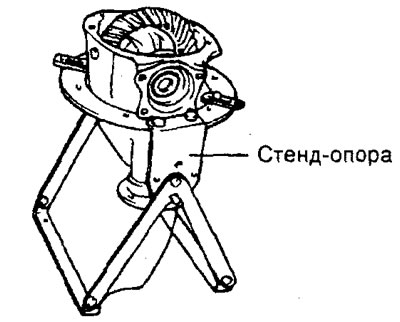
1. Using a dial gauge, measure the final drive gear runout.
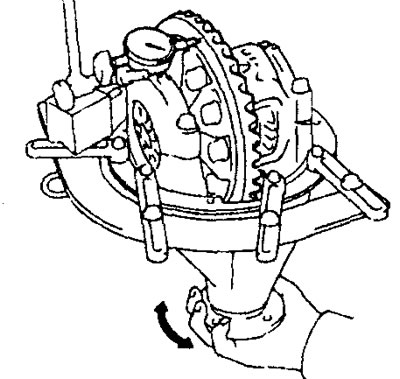
Maximum runout - 0.05 mm
If the amount of runout is out of specification, replace the drive and driven gears as a set.
2. Using a dial gauge, measure the backlash of the final drive gear teeth.

Lateral tooth clearance - 0.10 -0.15 mm
Note: Measure at least four teeth.
If the backlash of the final drive gear teeth is out of specification, adjust the side bearing preload or repair if necessary.
3. Checking the clearance in the meshing of the gears of the reducer.
A) Block the side gear from turning by inserting a wedge between the gear and the planet gear, measure the clearance in the engagement of the gears of the reducer with a dial indicator, placing the indicator rod nozzle on the planet gear.
Note: measure the gap at two or more points along the circumference of the satellite.
- Nominal value - 0 - 0.076 mm
- Maximum value - 2 mm
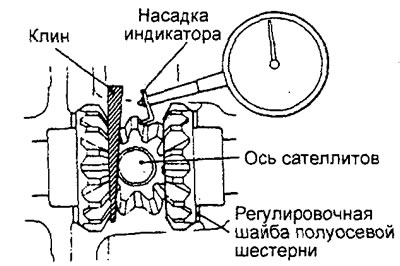
b) If the clearance in the engagement of the gears is greater than the maximum permissible value, then adjust it by replacing the adjusting spacers of the gearbox housing bearings.
Note: if it is impossible to adjust the clearance in the engagement of the gears of the reducer, then replace the side gears and pinions of the reducer as a set.
4. Checking the contact patch in the gearing of the final drive gears.
A) Apply a thin coat of Prussian Blue (or marking paint) on both side surfaces of the driven gear tooth.
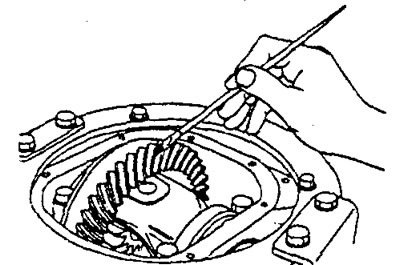
b) Insert bronze punch (special tool) between the gearbox housing and the gearbox and by hand turn the main gear drive gear by the flange first clockwise (in forward direction), then counterclockwise. During rotation, load the driven gear so that the torque applied to the final drive gear is approximately 2.5 - 2.9 Nm.
Attention: excessive number of revolutions of the driven gear leads to smearing of the contact patch and difficulties in identifying the engagement condition.
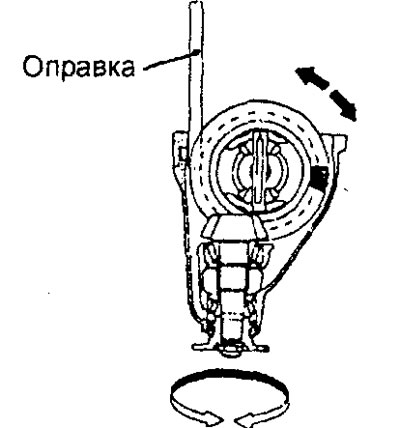
V) Check the contact patch on the teeth of the driven and driving gears of the final drive.
Note:
- A contact patch test is performed to confirm that the drive gear position is correctly adjusted (the location of the drive gear relative to the driven) and engagement gap. If necessary, readjust the position of the drive gear and the gap in the engagement to achieve the required contact patch in the engagement of the final drive gears.
- If it is not possible to adjust the engagement contact patch, then the driving and driven gears are worn out beyond the maximum allowable values, replace the final drive gear set.
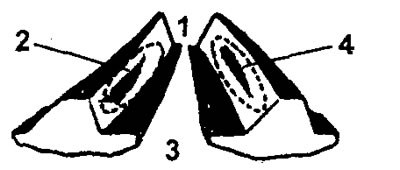
Normal shape of the contact patch. 1 - heel, 2 - leading side, 3 - heel, 4 - driven side.
G) If the drive gear is high, then the drive gear is too far from the center of the driven gear. In this case, increase the thickness of the drive gear shim to bring the drive gear closer to the center of the driven gear, or move the driven gear away from the drive gear to adjust the backlash.
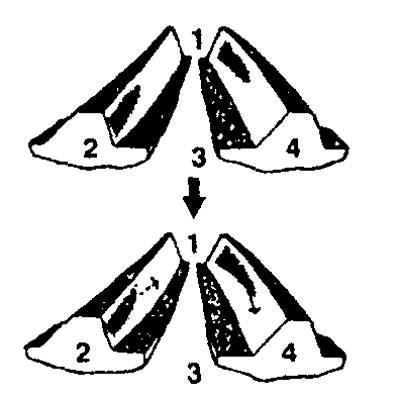
d) If the drive gear is low, then the drive gear is too close to the center of the driven gear. Reduce the thickness of the shim to set the drive gear further from the center of the driven gear, or to adjust the backlash, move the driven gear towards the drive gear.
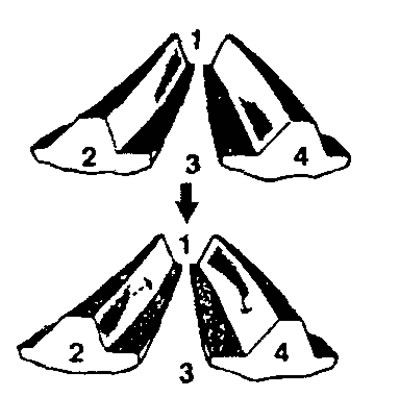
5. Check the oil seal for wear or deformation.
6. Check bearings for wear or discoloration due to overheating.
7. Check the gearbox housing for cracks.
8. Check the drive and driven gears for wear or cracks.
9. Check side gears, pinion gears and pinion shaft for wear or damage.
10. Check the gear side gear splines for excessive wear or damage.
Disassembly
Note: Perform the following checks before disassembly.
- Checking the clearance in the gear engagement of the final drive.
- Checking the runout of the final drive gear.
- Checking the clearance in the engagement of the gears of the gearbox.
- Checking the contact patch in the gearing of the final drive gears.
When removing parts, refer to the figure "Disassembly and assembly of the rear gearbox".
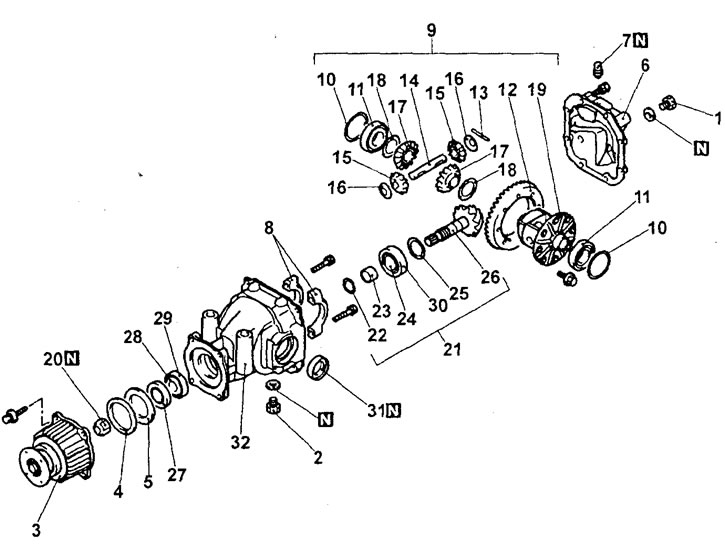
Disassembly and assembly of the rear gearbox. 1 - filler plug, 2 - drain plug, 3 - viscous coupling, 4 - spring washer, 5 - spacer, 6 - gearbox cover, 7 - breather, 8 - bearing caps, 9 - differential, 10 - side bearing spacer, 11 - side bearing, 12 - pinion gear, 13 - locking pin, 14 - pinion axle, 15 - pinion gear, 16 - pinion thrust washer, 17 - side gear, 18 - side gear thrust washer, 19 - differential housing, 20 - lock nut, 21 - final drive gear assembly, 22 - shim, 23 - bushing, 24 - rear bearing inner race, 25 - shim, 26 - pinion gear, 27 - oil seal, 28 - front bearing inner race, 29 - outer front bearing ring, 30 - rear bearing outer ring, 31 - oil seal, 32 - gearbox housing.
Caution: Be careful when removing the differential housing assembly, perform the removal operation slowly and carefully so as not to drop or damage the outer bearing races of the differential housing.
Note: Store the right and left differential housing bearings separately so that they are not mixed up during assembly.
Assembly
When installing parts, refer to the figure "Disassembly and assembly of the rear gearbox".
Note: Pay attention to the lubrication and locking adhesive points before installing the parts in the gearbox housing (see picture "Application points for lubrication and sealant").
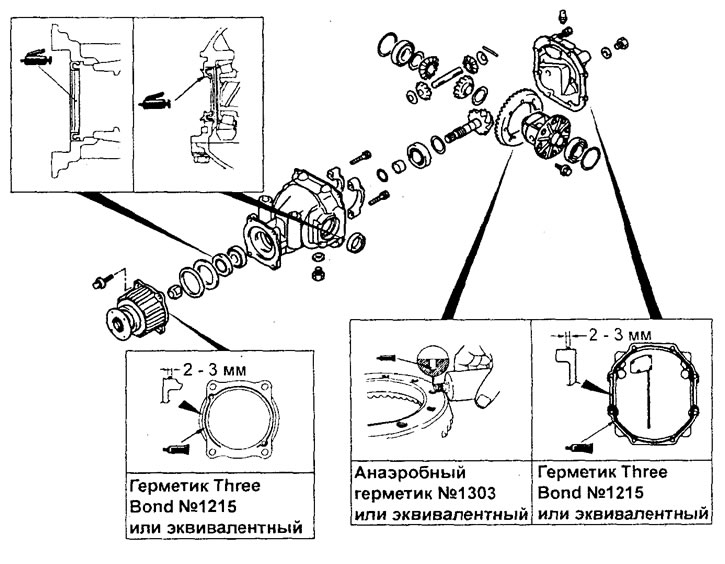
Application points for lubrication and sealant.
Attention: when adjusting the clearance, try to select the minimum number of adjusting spacers for each bearing of the differential housing.
Installation
Installation of details is made in an order, the return to removal.
After completing the installation of the parts, perform the following operations:
- A) Install rear anti-roll bar (see chapter "Suspension").
- b) Install the rear drive shafts (see section "Rear drive shafts").
- V) Install the elements of the exhaust system (see chapter "Intake and exhaust systems"),
- G) Pour oil into the gearbox housing.
Bushing replacement
1. Using the special tool, press out the bushings.
2. When pressing the bushings, follow the drawings.
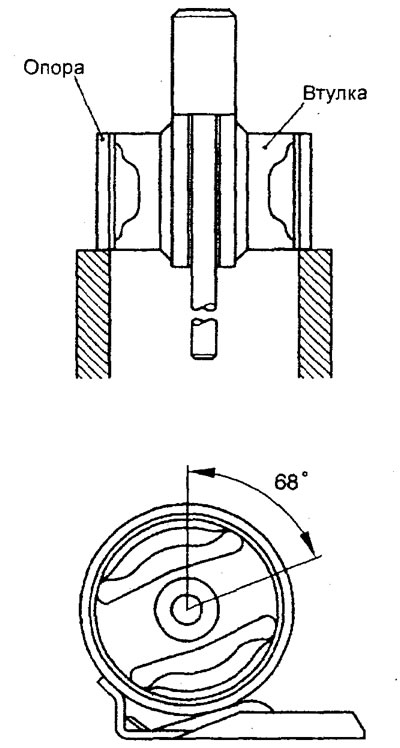
Gearbox mount.
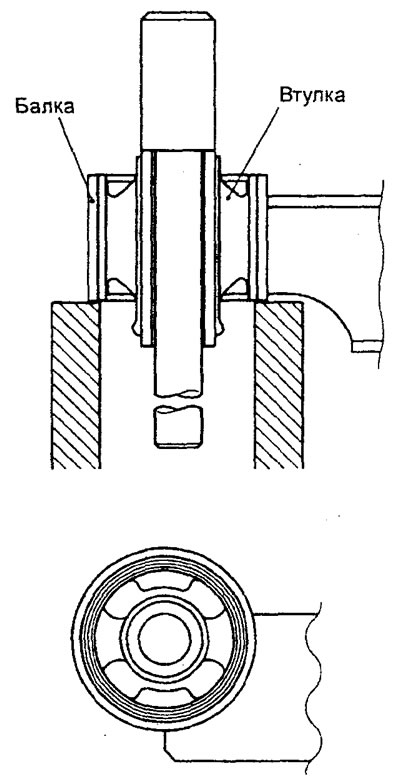
Gearbox mount.