Removing
Attention: on models with an additional passive safety system (SRS) before removing the steering gear, set the front wheels to the straight-ahead position and remove the key from the ignition. Failure to comply with these conditions may result in damage to the SRS coiled wire and unauthorized deployment of the airbag, which in turn will result in serious injury.
Removal of parts is carried out in the order of the numbers indicated in the figure "Steering gear".
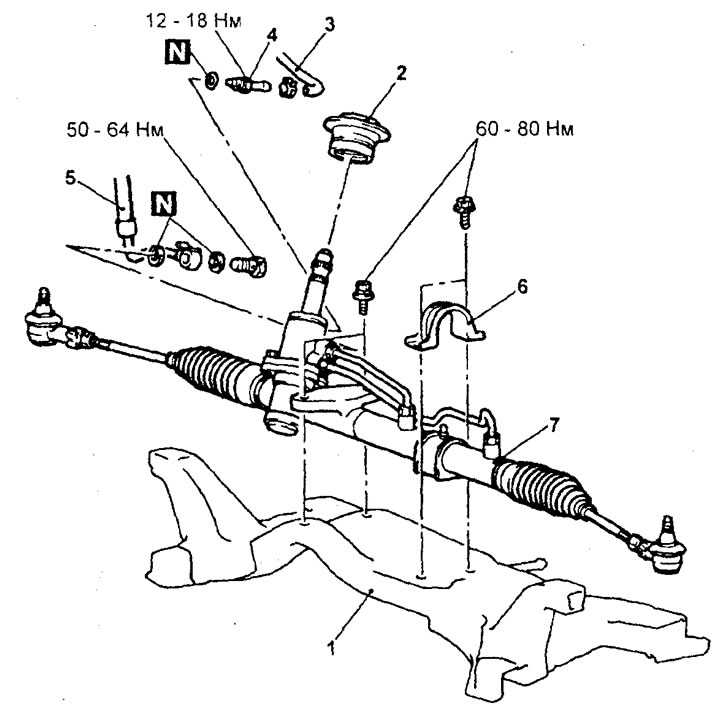
Steering gear. 1 - subframe, 2 - spacer, 3 - return hose connection, 4 - return tube, 5 - pressure hose connection, 6 - steering gear mounting bracket, 7 - steering gear assembly.
Before removing parts, drain the power steering fluid from the power steering hydraulic system.
When removing parts, pay attention to the following operations.
1. Disconnecting the tie rod end from the steering knuckle.
Attention:
- To prevent the puller from jumping off, you must first tie it with a cord.
- Just loosen the fastening nut on the ball joint pin, do not unscrew the nut completely.
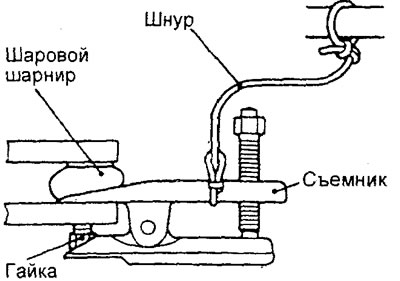
2. Removing the steering gear assembly.
Attention: when removing the steering gear assembly, remove the steering gear slowly and very carefully so as not to damage the tie rod boot and the tie rod end ball joint boot.
Steering gear disassembly
− Removal of parts is carried out in the order of numbers indicated in the figure "Steering gear disassembly".
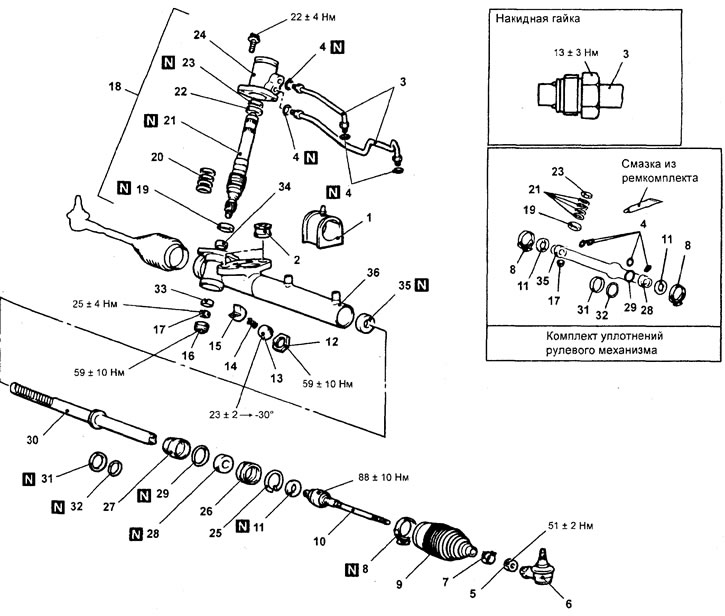
Steering gear disassembly.1 - steering gear housing support bushing, 2 - steering gear housing side support bushing, 3 - injection tube, 4 - O-ring, 5 - lock nut, 6 - tie rod end, 7 - protective boot clamp, 8 - protective boot band clamp, 9 - protective cover, 10 - steering rod, 11 - lock washer (when installing, adjust the total scroll torque of the drive gear), 12 - lock nut, 13 - rack stop cover, 14 - rack stop spring, 15 - rack stop, 16 - end cap, 17 - lock nut, 18 - valve body assembly, 19 - bottom gland, 20 - o-rings, 21 - drive gear and valve assembly, 22 - upper bearing, 23 - upper gland, 24 - valve body, 25 - retaining ring, 26 - rack travel stop, 27 - rack support bushing, 28 - stuffing box, 29 - O-ring, 30 - rack assembly, 31 - piston ring, 32 - ring gasket, 33 - lower bearing, 34 - needle bearing, 35 - oil seal, 36 - steering gear housing.
When removing parts, pay attention to the following operations.
1. Removing the rack stop cover.
Using the special tool, remove the rack stop cover from the steering gear housing.
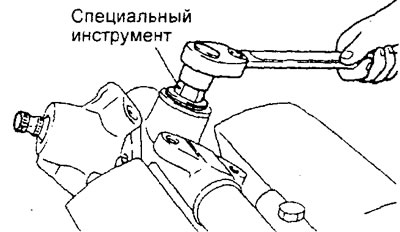
2. Removing the oil seal, pinion and valve assembly.
Gently tap the pinion gear off with a plastic-faced hammer.
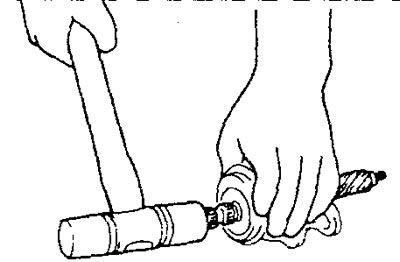
3. Removal of sealing rings.
Cut the o-ring and remove it from the pinion and valve assembly and from the rack.
Caution: When cutting the O-rings, be careful not to damage the pinion gear and valve assembly or rack.
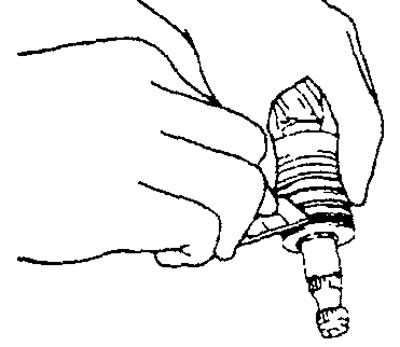
4. Removing the ball bearing and oil seal.
Using a mandrel and a plastic-faced hammer, simultaneously knock out the stuffing box and ball bearing from the valve body.
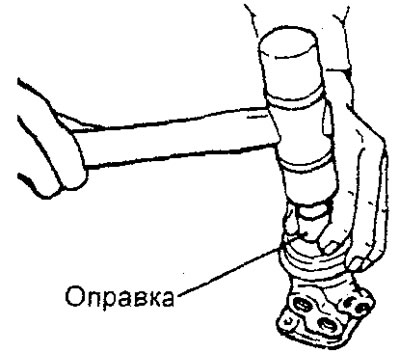
5. Removing the retaining ring.
A) Turn the rack travel stop clockwise until the end of the retaining ring comes out of the slot in the steering gear housing.
b) Turn the rack travel stop counterclockwise and remove the retaining ring.
Caution: Be aware that if you first turn the rack travel stop counterclockwise, the retaining ring will hit the groove in the steering gear housing and prevent the rack travel stop from turning.
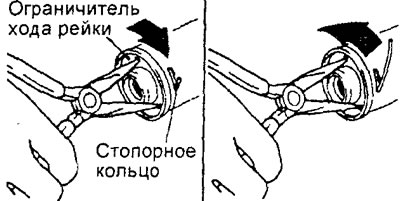
6. Removing the rack travel stop, rack support sleeve, rack and gland.
A) Carefully remove the rack assembly and remove the rack travel stop and support sleeve at the same time.
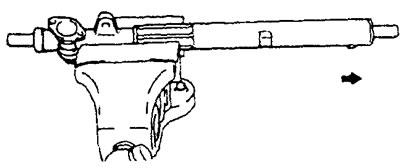
b) To remove the oil seal from the rail support sleeve, slightly bend the oil seal with a screwdriver.
Attention: do not damage the seating surface under the oil seal in the rack support sleeve.
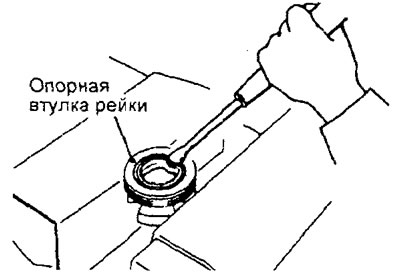
7. Removing the ball bearing.
Use a special tool or a brass drift to remove the ball bearing from the steering gear housing.
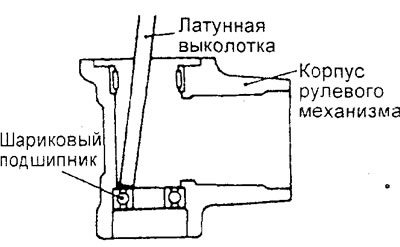
8. Removing the needle bearing.
Using the special tool, remove the needle bearing from the steering gear housing.
Attention: do not allow the special tool to be opened unnecessarily, so as not to damage the inner surfaces of the steering gear housing.
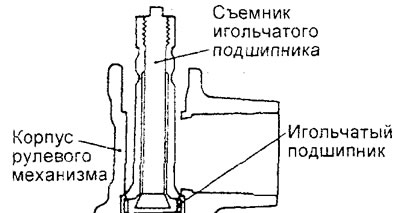
9. Removing the gland.
Using a piece of suitable pipe, remove the oil seal from the steering gear housing.
Attention: do not damage the inner surface of the rack cylinder in the steering gear housing.
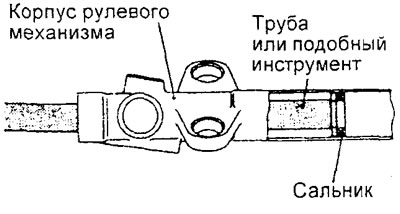
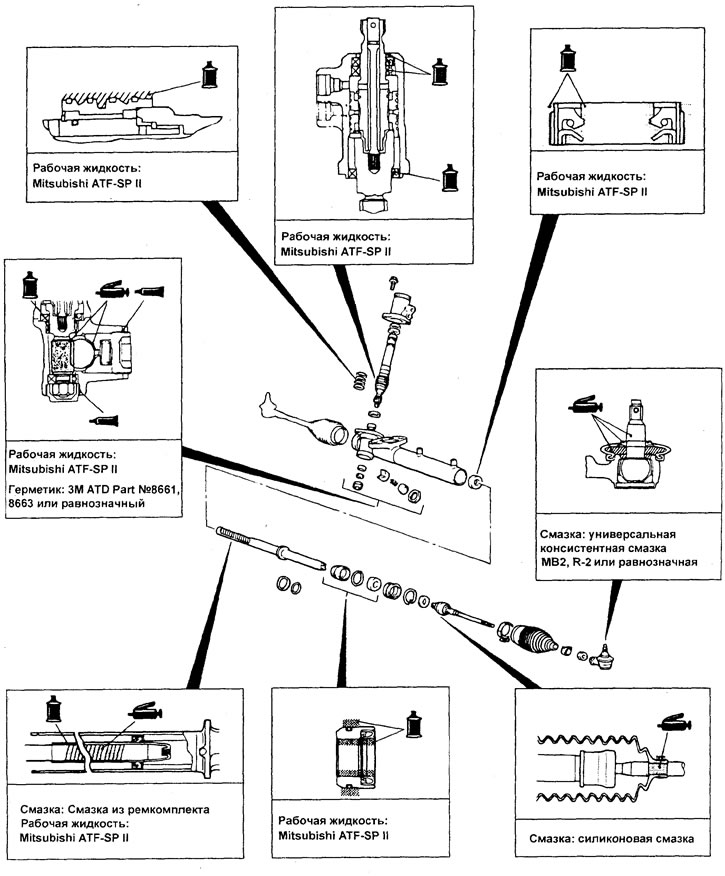
Map of application points for lubrication, working fluid and sealant.
Check before assembly
1. Steering rack.
A) Check for wear on the steering rack teeth.
b) Check for excessive wear on the seal faces.
V) Check the straightness of the steering rack.
2. Drive gear and valve assembly,
A) Check the drive gear teeth for wear or damage.
b) Check the O-rings for wear or damage.
3. Bearing.
A) Check the smoothness of rotation and the absence of extraneous noise during the operation of the bearings.
b) Check for play in the bearings.
V) Check that the needles are not falling out of the needle bearing.
Other checks.
A) Check for damage to the inner surface of the steering gear housing cylinder.
b) Check protective covers for wear, cracks or tears.
V) Check the rack stop for excessive wear or dents.
G) Check the steering rack bearing bush for excessive wear or damage.
Assembly
Installation of parts is carried out in the reverse order of removal.
Pay attention to the following operations when installing parts.
1. Installing the gland.
Install as shown in the figure.
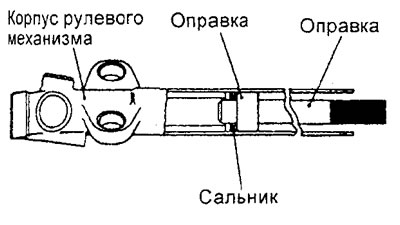
2.Install needle bearing and ball bearing.
Install as shown in the figure.
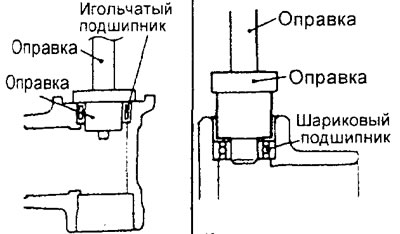
3. Rail installation.
A) Lubricate the steering rack teeth with grease from the repair kit.
Attention: do not clog the ventilation hole in the rail with grease.
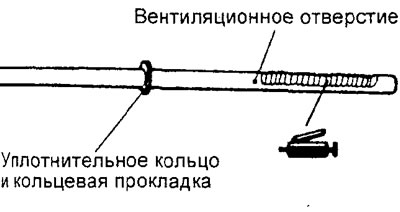
b) Cover the surface of the teeth with a special tool.
V) Lubricate the special tool with working fluid.
Recommended Fluid - Mitsubishi ATF-SPII
Attention: do not use ATF-SP II M and ATF-SP III fluid in steering.
G) Align the axis of the O-ring hole and the steering rack to prevent slipping out of the retaining ring, and slowly insert the steering rack from the side of the power cylinder.
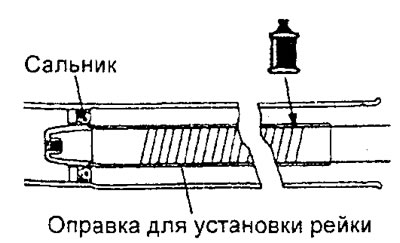
4. Installation of the stuffing box and the supporting sleeve of the rail.
A) Lubricate the outer surface of the stuffing box with working fluid. Using a special tool, press the oil seal flush with the end face of the rack support sleeve.
Recommended Fluid - Mitsubishi ATF-SP 11
Attention: do not use ATF-SP II M and ATF-SP III fluid in steering.
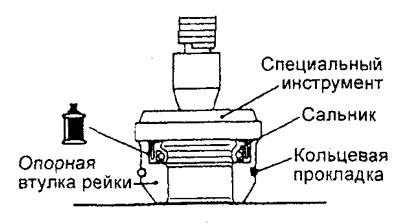
b) Lubricate the inner surface of the stuffing box and the O-ring with working fluid.
Recommended Fluid - Mitsubishi ATF-SP II
Attention: do not use ATF-SP II M and ATF-SP III fluid in steering.
V) Wrap tape around the tip of the rail and slide the support sleeve onto the rail.
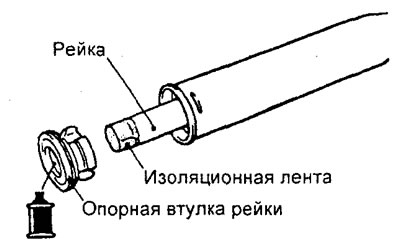
V) Wrap tape around the tip of the rail and slide the support sleeve onto the rail.
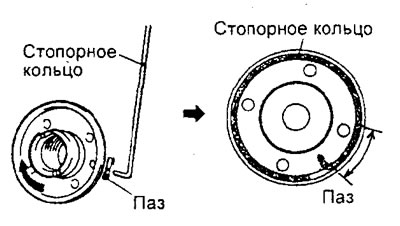
6. Installation of the stuffing box.
Lubricate the outer surface of the stuffing box with working fluid. Using the special tools, press the gland into the valve body.
Recommended Mitsubishi ATF-SP II Fluid
Attention: do not use ATF-SP I M and ATF-SP III fluid in steering.
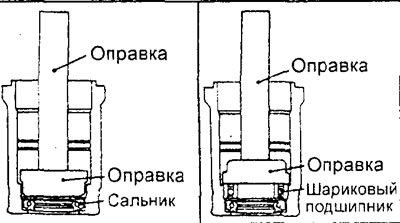
7. Installation of the ball bearing.
Lubricate the outer race of the bearing with operating fluid. Using special tools, press the bearing into the valve body.
Recommended Fluid - Mitsubishi A TF-SP II
Attention: do not use ATF-SP I M and ATF-SP III fluid in steering.
8. Installation of the sealing ring,
A) Knead the o-ring to soften it.
b) Lubricate the O-ring with the recommended fluid and insert it into the rack groove.
Recommended Fluid - Mitsubishi ATF-SP II
Attention: do not use ATF-SP II M and ATF-SP III fluid in steering.
V) Insert the cone of the special tool from the pinion side and squeeze the O-ring.
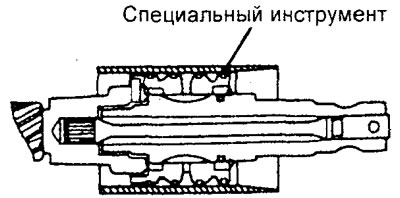
9. Installation of the stuffing box.
Using the special tool, press the gland into the valve body.
Attention: the upper end of the stuffing box should protrude above the end of the valve body by approximately 1 mm. Mounting the packing flush with or below the valve body end may result in fluid leaks and will require reassembly.
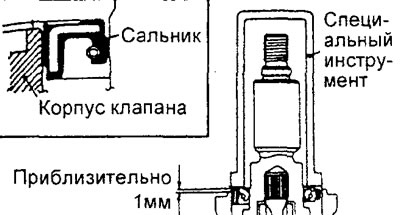
11. Installing the plug.
A) Apply the specified sealant to the threads of the plug.
Sealant - Three Bond #1215 or equivalent
b) After tightening the plug, mint it at two points using a core.
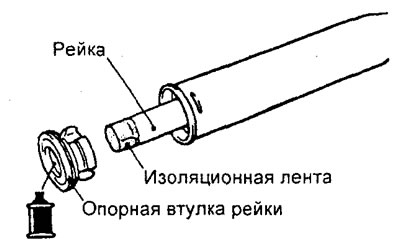
12. Install the rack stop cover and locknut.
A) Set the rack to its center position. Tighten the rack stop cover to the specified torque using the special tool.
Tightening torque - 15 N.m
b) Loosen the rack stop cover about 30 degrees.
V) Fix the rack stop cover with the special tool and tighten the lock nut.
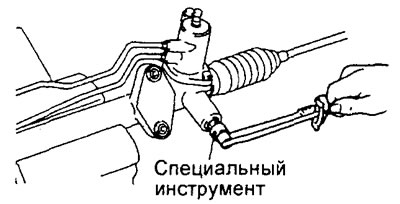
13. Adjustment of the total moment of scrolling the drive gear.
A) Using a special wrench, turn the gear one revolution in 4 to 6 seconds and check the amount of scroll torque and the amount of scroll torque deviation during gear rotation.
Nominal value - 0.6 -1.6 N.m
Tolerance - 0.4 N.m
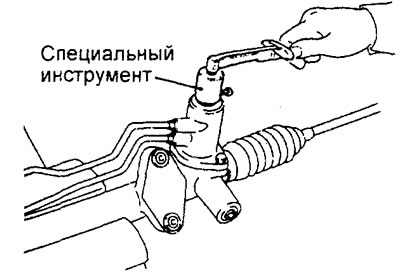
b) If the value of the scroll torque and the value of the torque deviation do not correspond to the nominal values, then unscrew the rack stop cover by 0 - 30 degrees and adjust the scroll torque.
Attention:
- In the process of adjustment, try to set the upper limit of the nominal value.
- Make sure that there are no knocks and jams when moving the steering rack.
- The total scrolling moment must be measured throughout the rack travel.
Note: If the pinion gear torque cannot be adjusted by turning the rack stop cover a certain angle, check or replace the rack stop and rack stop cover parts.
V) After completing the adjustment, secure the rack stop cover by tightening the locknut.
14. Installing the tie rod and lock washer.
After installing the steering rod on the rack, insert the antennae of the lock washer in two places into the notches of the steering rod.
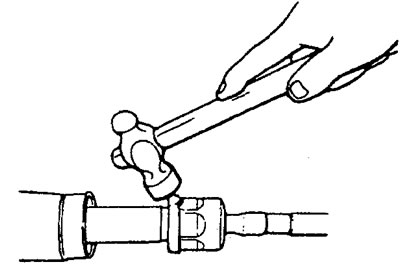
15 Installing the protective boot strap.
A) Turn the adjusting bolt of the special tool to adjust the size "W" up to the nominal value.
Nominal value - W 2.9 mm
Attention:
- If the size is more than 2.9 mm, then tighten the bolt.
- If the size is less than 2.9 mm, then turn off the bolt.
Note:
- One turn of the adjusting bolt changes the size "W" approximately 0.7 mm.
- Do not turn the adjusting bolt more than one turn.
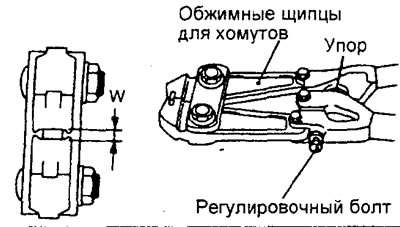
b) Using a special tool, crimp the protective boot clamp band.
Attention:
- Fasten the rack housing, and crimp the band clamp securely.
- Crimp the band clamp until the tool handle rests against the stop.
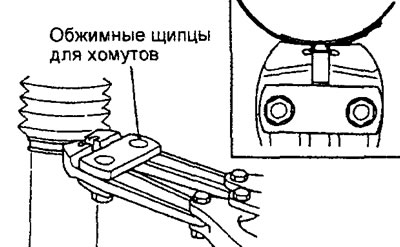
V) Check clamp width (size "A") and its compliance with the nominal value.
Rated value "A" - 2.4 - 2.8 mm
Attention:
- If size "A" larger than 2.8 mm, then re-adjust the size "W", as indicated in paragraph (A), up to the value determined by the specified formula (W = 5.5 mm - A), o repeat the operations of paragraph (b) (for example, if A = 2.9 mm, then W = 2.6 mm).
- If size "A" less than 2.4 mm, then remove the band clamp, re-adjust the 'W'' dimension as indicated in s paragraph (A), up to the value determined by the indicated formula (W = 5.5 mm - A), install a new band clamp and repeat steps (b) And (V) (for example, if A = 2.3 mm, then W = 3.2 mm).
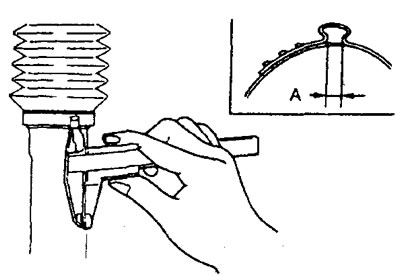
16. Installing the tie rod end and the tie rod end locknut.
A) Screw the left and right tie rod ends to the size shown in the figure.
Rated value "A" - 181 mm
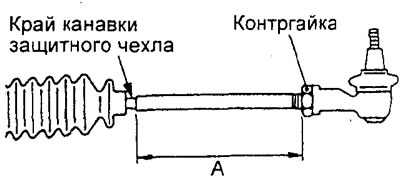
b) Lock in position with locknut
Attention: finally tighten the locknuts of the tie rod ends only after installing the steering mechanism on the vehicle and adjusting the front wheel toe-in.
17. Installing the protective cover of the ball joint.
Note: The protective cover is only replaced if it is damaged during installation.
A) Fill the inside of the protective boot with multipurpose grease.
b) Apply the specified sealant to the sealing lip of the protective boot.
Sealant - Three Bond #1215 or equivalent
V) Using the special tool, install the protective boot on the ball joint pin of the tie rod end.
G) Hold the ball joint boot with your finger and check that it is not cracked or otherwise damaged.
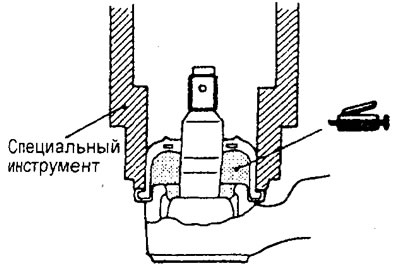
Check before installation
1. Check the rubber parts for cracks and damage.
2. Check up the general moment of rotation of a leading gear wheel of the steering mechanism.
A) To check the total rotation torque of the steering gear, use a special wrench to rotate the rack and pinion steering gear within one revolution for 4-6 seconds.
Nominal value - 0.6 - 1.6 Nm
Tolerance - 0.4 N.m
Note:
- Remove the protective covers from the steering gear housing before checking.
- − Measure the drive gear torque by turning the drive gear left and right 180 degrees (full travel of the steering rack).
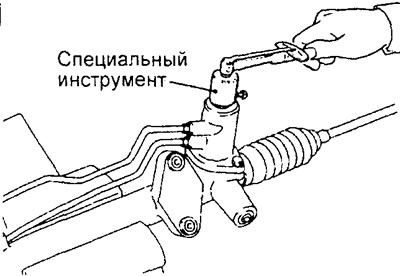
6) If the measured value does not correspond to the nominal value, first adjust the position of the steering rack stop cover, and then check the total torque of the steering gear again.
V) If the total drive gear torque cannot be adjusted, check the steering rack stop cover, the steering rack stop spring, the steering rack stop and replace parts if necessary.
Attention: when installing the steering mechanism in a vise, clamp it only at the attachment points. Clamping the steering gear in any other way could damage or deform the steering gear housing.
3. Check up resistance to rotation of the hinge of steering draft.
A) Make 10 strong turns of the tie rod end.
b) Using a spring dynamometer, measure the resistance to rotation of the tie rod joint (moment of resistance to rotation).
Rated value - 6 - 19 N (1.5 - 4.9 N.m)
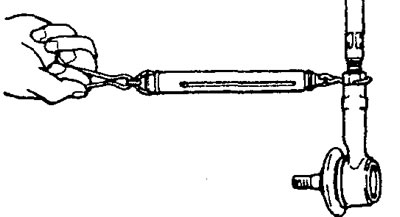
V) If the measured value exceeds the nominal value, then replace the tie rod.
G) If the measured value is less than the nominal value, but the tie rod turns smoothly, without excessive play, then such a tip is suitable for operation.
4. Check up a protective cover of a spherical hinge of a tip of steering draft.
A) Hold the ball joint boot with your finger and check that it is not cracked or otherwise damaged.
b) If the protective cover is cracked or otherwise damaged, it must be replaced.
Note:
- Cracks or other damage to the protective boot can damage the ball joint. Therefore, if the protective cover is damaged during the repair process, it must be replaced.
Installation
Installation of parts is carried out in the reverse order of removal.
After installing the parts, perform the following operations.
A) Check up a protective cover of a spherical joint of a tip of steering draft. Hold the tie rod end with your finger and check for cracks or other damage.
b) Pour working fluid into the booster hydraulic system.
V) Bleed air from power steering hydraulic system.
G) Check the middle position of the steering wheel when the wheels are parallel to the longitudinal axis of the vehicle.
d) Check and, if necessary, adjust the angles of the front wheels.