Attention: Diesel engines require a compression gauge with large measuring ranges up to approx. 40 bar. The difference in compression between the individual cylinders must not exceed 1.0 bar (diesel engine: 3.0 bar). If the compression of one or more cylinders differs from the compression in others by more than 1.0 bar (diesel engine 3.0 bar) you can suspect a defect in the valves, wear of the piston rings or cylinder mirrors. When the wear limit is reached, the engine must be overhauled or replaced.
Compression pressure in bar
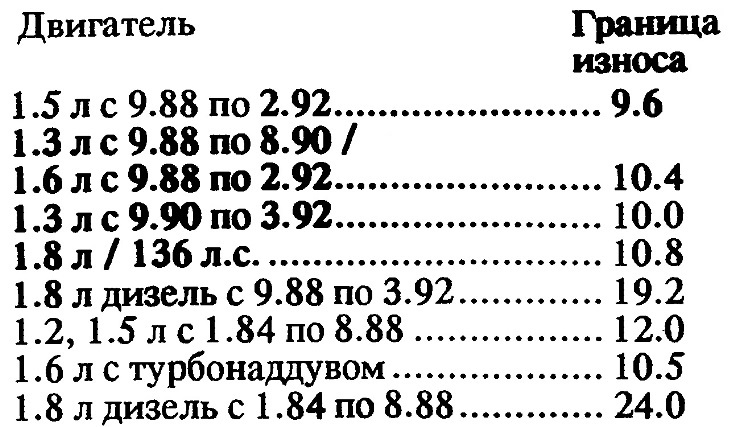
Warm up the engine to operating temperature. To do this, drive the vehicle up to the normal operating temperature of the coolant. The reading should be 80°+ 90°C.
Switch off the ignition.
Gas engine
Remove the ignition wires from all spark plugs. Special tongs are available for this purpose, for example, HA-ZET 1849. However, they can only be handled by metal sleeves, if any.
Disconnect the ignition wires from the ignition coil.
Engine with fuel injection device: Remove power from the fuel pump, remove the relay connector. See 8.8 for relay location.
Blow out the candle niches with compressed air and remove all the candles.
Crank the engine several times with the starter to throw out residue and soot.
Attention: Set the gearbox to neutral, cock the handbrake. When cranking the engine, do not lean over the spark plug holes, risk of injury from the ejected coolant or oil, (with defective cylinder walls). For safety reasons, cover the spark plug holes with a rag.
Insert or screw a compression gauge into the spark plug hole in accordance with the instruction manual.
Have an assistant press the gas pedal. During the entire test, the gas pedal must be depressed.
Operate the starter to crank the engine about 8 revolutions until the compression gauge reaches its maximum value.
Check all cylinders one by one, compare with the specified value.
If the compression is below the wear limit, pour some oil into the spark plug holes and repeat the compression test. If compression increases after adding oil, piston rings and/or cylinder walls may be worn. If compression does not increase, the valve or cylinder head gasket is usually defective.
Screw in the spark plugs and connect the ignition wires, see point 5/32.1.
Attach the ignition wire to the ignition coil.
Plug in the fuel pump relay connector.
Diesel engine
Remove upper intake manifold see point 1.10.
Disconnect the electrical wire from the high pressure fuel pump switch (injection pump).
Clean the injection pipes with a cleaner and remove them as a set, without disturbing their curvature, see clause 9.10.
Remove the injectors see clause 9.10.
Remove the holder gasket and nozzle seal from the injection hole.
Crank the engine with the starter to push out the residue and soot.
Attention: Set the gearbox to neutral, cock the handbrake. When cranking the engine, do not lean over the spark plug holes - risk of injury from escaping coolant or oil (with defective cylinder walls). For safety reasons, cover the holes with a cloth.
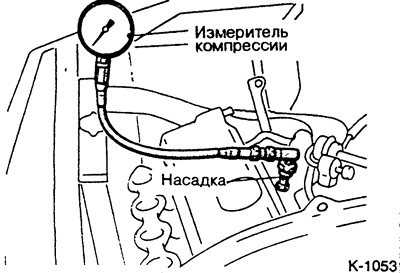
Screw the nozzle into the hole of the injection nozzle, then screw the compression gauge to the nozzle.
Have an assistant depress the gas pedal all the way down and keep your foot on the pedal throughout the test.
Crank the engine at starter speed (~ 250 rpm) until the instrument stops increasing.
Check the compression in all cylinders in sequence and compare with the specified value.
If the compression is below the wear limit, pour some oil into the injector holes and repeat the compression test. If compression increases after adding oil, piston rings and/or cylinder walls may be worn. If compression does not increase, the valve or cylinder head gasket is usually defective.
Install the injectors see section 9.10.
Install injection pipes.
Install the upper part of the intake manifold, see point 1.10.
Put the electrical wire on the injection pump switch.