General information
Most of the procedures for overhaul and reconditioning of the engine are among the so-called standard ones. Particular attention should be paid to strict compliance with the requirements of the Specifications for a particular engine. Much also depends on the qualifications of the performer. The compilers of this Guide recommend the following approach to preparing and performing engine rebuilds:
- The owner of the car can independently dismantle, clean and check the condition of the components;
- After acquiring the necessary replacement parts, all removed elements should be delivered to a car service workshop, where preparation for installation and assembly of components will be carried out by qualified specialists;
- Most assembly procedures (installation of the crankshaft, bearings, connecting rod and piston assemblies, etc.) can also be produced on the owner's own, subject to the availability of the necessary tools.
Before starting work, try to determine for yourself the range of work that you will do yourself.
Tools
Among the tools, the use of which is a prerequisite for a complete engine overhaul includes the following:
- Standard set of locksmith tools;
- A set of cardboard or plastic containers/plastic bags for organized storage of small components;
- Set of screw and leg type pullers;
- Scraper for cleaning mating surfaces;
- Valve spring compression tool;
- Tool for cleaning grooves for installing piston rings;
- Tool for removing and installing piston rings;
- Special countersink for removal of stepped wear from cylinder walls;
- Hone for processing cylinder mirrors;
- Micrometer set;
- Telescopic caliper;
- Plunger Type Dial Meter (DTI);
- Plastigage set for determining operating clearances in bearings;
- Portable mounting stand for fixing the engine removed from the car (desirable);
- Electric drill;
- A set of taps and lerok;
- Wire brushes;
- Cylindrical brushes for cleaning oil galleries;
- Solvent.
Sometimes it becomes necessary to use some special tools, the identification number of which in such cases is indicated in the text of the description of the corresponding procedure.
Materials used for the manufacture of components and parts of the power unit
Recently, aluminum has become increasingly popular in the automotive industry due to its low specific gravity. Some special precautions should be observed when servicing aluminum parts:
- Do not use aggressive solutions for cleaning aluminum parts, the use of which can lead to alloy erosion;
- Before dry cleaning the power unit, remove all aluminum components from it;
- To avoid "tacking" screwed into fasteners made of aluminum, pre-lubricate its threaded part with engine oil or anti-seize sealant;
- Try not to over tighten fasteners screwed into aluminum components with excessive force - follow the requirements of the Specifications.
When assembling the unit, all moving internal components should be lubricated with a special lubricant before installation, which ensures gentle operation during initial start-up (engine oil is not suitable for lubricating such components).
Threaded fasteners subjected to high vibration loads should be secured with a special non-hardening sealant such as Loctite®.
Cleaning
Before checking the condition of engine components, they must be thoroughly cleaned. Remember that cracks in the casting of the block / cylinder head can easily be seen under the layer of deposits, scale and soot that are inevitably present on the surface of these components.
Components can be cleaned using conventional plumbing tools and various solvents and detergents. The main layer of coal deposits is usually removed by chipping with a special wooden chisel. Carbon deposits and traces of old gasket material are removed with a scraper and solvent. To remove particularly hard deposits, you can use special nozzles for an electric drill, however, you should act very carefully so as not to accidentally damage the gasket surfaces, bearing beds and cylinder mirrors.
Attention! The compilers of this Guide recommend avoiding the use of wire attachments to an electric drill for cleaning surfaces made of aluminum assemblies and engine parts!
Always try to follow the cleaning agent and tool manufacturer's instructions. Remember to wear safety goggles and gloves.
Before cleaning the cylinder block, remove all designed plugs, squeeze plugs and pressed bearing shells from it. For flushing hard-to-reach cavities, galleries and oil flows, use special brushes.
Do not forget that all the smallest components of the unit, including fasteners and springs, should be subject to reading. To dissolve traces of corrosion and various kinds of deposits, small parts should first be placed in an oil bath.
Pay special attention to removing carbon deposits from the piston bottoms from the grooves for installing the piston rings.
Attention! In no case do not use metal brushes and nozzles for an electric drill to clean the pistons!
When cleaning the cylinder head, carefully remove carbon deposits from the walls of the combustion chambers.
Attention! Cleaning is carried out before removing the valves, which avoids the risk of accidental damage to their seats!
In the absence of complete self-confidence, it would be reasonable to entrust the cleaning of engine components to car service specialists.
Restoration of damaged threaded holes
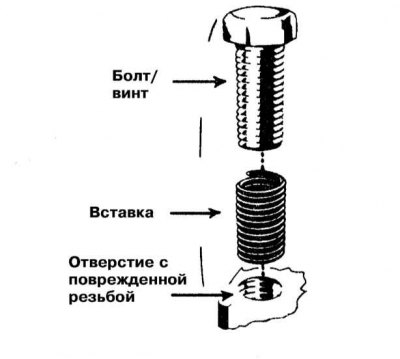
There are several methods for repairing damaged threaded holes. Each of them is based on reaming, during which the damaged turns of the old thread are completely removed. Then a new thread is applied into which a special twisted insert is screwed, allowing you to save the original dimensions of the fastener.
Twisted inserts are available for threaded fasteners of standard (American) and metric (European) type. Separate inserts are used to restore threads in spark plug holes. The inserts are equipped with special locking tabs that ensure their fixation on the setting tool during installation. After the insert is screwed in, the tongue is bitten off.
![]() | ![]() |
A typical set for repairing threaded holes includes a set of twisted inserts, a tap that matches the external thread of the inserts, and a device for seating the inserts in the hole. Kits for restoring threads in candle holes are somewhat different from the usual ones due to the need to use taps with guide turns and a countersinking front face. Kits must be accompanied by detailed instructions for use. If you are not confident in your own abilities, do not hesitate to seek help from car service specialists.
For extracting from threaded holes "stuck" fasteners are usually used self-locking tongs - before eversion, the fasteners should be impregnated with a penetrating compound.